Protecting Metal Parts from Corrosion
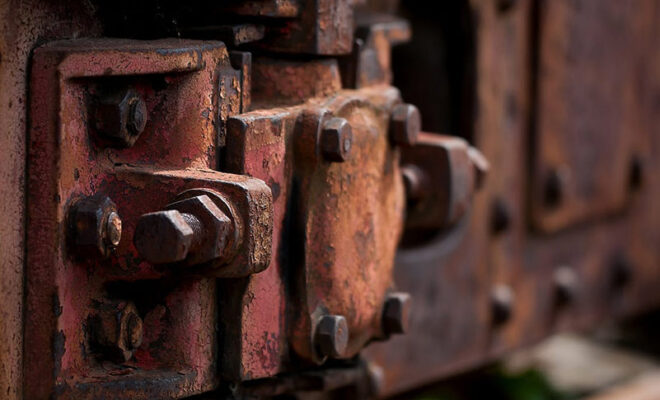
Corrosion is a perennial problem when discussing metal parts. When a metal surface corrodes, it doesn’t just damage the equipment itself, but it’s also dangerous to employees. Without corrosion protection coating applied to metal surfaces, you your equipment longevity is reduced and teammates are exposed to fumes that may result from oxidation.
But here’s good news for you: The damaging forces of corrosion can be prevented. One of the most cost-effective solutions available today to coat metal parts is electroless nickel plating.
Electroless Nickel Plating: What Is It And How Does It Work?
Electroless nickel plating, or ENP, is an autocatalytic process of depositing nickel-based alloys onto a metal surface.
A metal finishing company in Texas that offers this service doesn’t need to use any external power source, like sources of electric current. Instead, they’d need a water solution with a reducing agent where they will “bathe” the material to be coated. The chemical process itself will result in a deposition of a nickel alloy and phosphorus onto the surface of the metal part being bathed.
Experts in wear resistant steel coatings in Texas recommend ENP for its cost-effective advantages and the strong bond the coating has with the metal part.
First and foremost, a nickel-based alloy is versatile. It can protect substrates from atmospheric corrosion, seawater, petroleum, and high-temperature environments. If your equipment is exposed to corrosive elements, ENP is recommended for the metal components your equipment manufacturer may use.
Additionally, it can be used to coat various types of materials, from steel, aluminum, stainless steel and most reflective metals. Whether the material takes a regular shape or has more complex geometries, ENP can deposit nickel-based alloyuniformly. Some metal finishing companies can even coat materials that are 40 feet long.
ENP enhances hardness and guarantees lasting adhesion, subsequently minimizing wear and tear. This allows plant employees like you to utilize the coated materials throughout their intended service life fully.
Protecting Metal Substrates Against Corrosion
If you’re working in a manufacturing plant, wear resistant steel coatings will help minimize or even eliminate corrosion concerns.
Though you shouldn’t be complacent in carrying out your tasks and undertaking safety measures (e.g., wearing protective equipment), you can have peace of mind knowing that the metal parts you’re working with are well-protected from corrosive substances.
When hiring an electroless nickel plating shop in TX, manufacturing plant owners can choose from various types of protection. And this is dependent on how much phosphorus is present in the nickel-based alloy.
Low phosphorus. With phosphorous content of no more than 5%, this process produces that hardest-coated output. Nonetheless, they tend to have the weakest corrosion-resisting properties. Among the three options, this is the least in demand.
Medium phosphorus. Most metal plating companies use mixtures up to 10% phosphorus. Apart from offering a faster plating time, they produce better solderability and have a higher melting point. They can accommodate heat of up to around 1,000 degrees Celsius.
High phosphorus. Containing up to 13% phosphorus, this offers the best resistance against corrosion although difficult to find electroless nickel plater for these high phosphorus concentrations. It’s also the most ductile — allowing the coated material to be less prone to breakage and brittle damage. The downside, however, is that it takes longer to finish. Therefore, ENP superior to any chrome plating solution in Dallas but your options of plating shops are fewer.